Деревообрабатывающее производство
Деревообрабатывающие производства играют ключевую роль в промышленности, обеспечивая обработку древесины для создания разнообразной продукции. Рассмотрим основные типы таких производств, их особенности и применение.
Лесопильные заводы — это предприятия, где происходит первичная обработка древесины. Здесь бревна распиливают на доски, брусья и другие пиломатериалы. Современные лесопильные заводы оснащены высокотехнологичным оборудованием, позволяющим максимизировать выход продукции и минимизировать отходы.
Фанерные заводы — специализируются на производстве фанеры, материала, состоящего из нескольких слоёв древесины, склеенных под давлением. Фанера широко используется в строительстве, мебельной промышленности и для упаковки.
Заводы по производству ДСП и МДФ — эти предприятия производят древесно-стружечные и древесно-волокнистые плиты соответственно. ДСП и МДФ используются в мебельной промышленности и внутренней отделке помещений благодаря своей стойкости и легкости обработки.
Заводы по производству деревянных изделий — включают производство различных конечных продуктов, таких как мебель, двери, окна и декоративные элементы. Такие предприятия могут сочетать традиционные столярные техники с современными технологиями ЧПУ для создания уникальных изделий.
Предприятия по производству древесного угля — это заводы, где древесина подвергается процессу пиролиза для получения древесного угля, который используется в качестве топлива и фильтрующего агента.
Биоэнергетические заводы — на этих предприятиях из отходов древесины получают энергию, используя технологии сжигания или газификации. Это способствует утилизации отходов и производству возобновляемой энергии.
Заводы по производству целлюлозы и бумаги — занимаются переработкой древесины в целлюлозу, которая далее используется для производства бумаги и картонных изделий. Это одно из крупнейших направлений в деревообрабатывающей промышленности.
Эффективность деревообрабатывающих производств во многом зависит от использования современных технологий, автоматизации процессов и строгого контроля качества. Развитие этих предприятий способствует устойчивому управлению лесными ресурсами и минимизации экологического воздействия, что делает их важной составляющей промышленного и экономического роста.
Деревообрабатывающая отрасль
одна из наиболее трудоёмких индустрий лесопромышленного комплекса, продукция, которой находит повсеместное применение. Используя механическую и химическую обработку древесины, отрасль выпускает:
ТЕХНОЛОГИЯ ПРОИЗВОДСТВА БРУСА
Технологический процесс производства начинается на лесозаготовительных хозяйствах. Там выбирают наиболее подходящие по возрасту деревья, после чего их спиливают и на сортимент возах транспортируют на пилораму. Для производства бруса подойдут только деревья с ровным стволом, поэтому далеко не каждое дерево может в будущем стать строительным материалом. Все ветки удаляются непосредственно после спиливания дерева, так что на дальнейшую обработку отправляется только ствол. Ветки тоже идут в производство, но для других целей. Они могут в будущем стать дровами или будут перемолоты для создания топливных древесных гранул. При попадании на пилораму стволы сортируют по толщине и породам дерева, если в этом есть необходимость. Но зачастую в одной партии доставляются деревья одной породы и одного года высадки, так что они имеют примерно одинаковый диаметр.
Если планируется производство материала с минимальной влажностью, сырье отправляется в сушильные камеры, где в зависимости от его состояния может провести до нескольких недель, пока уровень влажности не будет понижен до установленной отметки. При изготовлении бруса естественной влажности этот этап пропускают и приступают сразу непосредственно к обработке. Не зависимо от того, какой формы брус будет на выходе, сначала каждый ствол попадает на станок, который снимает кору и верхний слой древесины.
После обработки заготовка имеет идеальную круглую форму без каких-либо впадин или выступов. Дальнейший процесс обработки зависит от вида производимого материала. При изготовлении обыкновенного бруса округлая заготовка поступает на оборудование для отпиливания круглых частей. На выходе получается прямоугольный параллелепипед. После этого он распиливается на доски установленных габаритов, упаковывается и отправляется на склад готовой продукции или сразу к заказчику.
Какие размеры бруса будут выбраны в качестве окончательного варианта зависит от технического задания. Современное оборудование дает возможность задать конкретные настройки с точностью до миллиметра, так что при выполнении индивидуального заказа у предприятия не возникнет трудностей. Станок для бруса, оцилиндрованной формы, придает всем заготовкам одинаковый диаметр. Параметры оператор задает вручную, а обработка идет полностью в автоматическом режиме. Это позволяет получать идеальный результат за короткое время.
После обработки и придания брусу нужного диаметра, он поступает на станок, который пропиливает на одной из сторон специальную канавку. При строительстве она служит для лучшей стыковки деталей между собой. Когда форма готова, производится шлифовка бруса до гладкого состояния. Профилированный материал имеет самую сложную и трудоемкую технологию производства. Начальные этапы полностью соответствуют изготовления обыкновенного бруса, но после получения формы параллелепипеда он отправляется не на склад, а на еще одну обработку. Из заготовок будут выпилены деревянные профили со специальными пазами. Для этого используются фрезы для бруса разной формы.
После обработки доски шлифуют до гладкого состояния и упаковывают. Профилированный брус очень хорош при строительстве различных объектов. Благодаря пазам конструкции собираются очень оперативно, не имеют между собой зазоров и не требуют использования монтажных материалов. Хотя последнее свойство зачастую игнорируют и для верности все равно скрепляют детали между собой специальными средствами.
Производство фанеры
Технология производства фанеры сегодня подразумевает минимальное использование ручного труда. Большинство операций в технологическом процессе проводится станками и роботизированными линиями. Но, даже при таком высоком уровне развития оборудования для производства фанеры без профессиональных кадров не обойтись.
Самые ответственные операции в процессе производства – отбор древесины, выбраковка, подбор качественного шпона проводится вручную. А вот среди необходимого оборудования для производства фанеры должны быть:
окорочной станок;
ванна для замачивания заготовок;
лущильный станок;
гильотина;
туннельная сушилка;
станок для нанесения клея;
линия для склеивания;
прессы для холодного и горячего склеивания;
форматно-раскроечный станок;
шлифовальная установка;
Это далеко не полный перечень оборудования для производства. Для расширения ассортимента продукции в перечень оборудования можно включить и станок лазерной резки материала, и станок для фасонной формовки изделий.
Заготовка древесины для получения фанеры.
Для получения продукции самого высокого качества требуется отбор самого качественного сырья. Лучшим сырьем считается липа и береза. Из лиственных пород получается продукция среднего качества. А вот из хвойных обычно получается продукт самого низкого качества, используемый в строительстве как технологический материал для опалубки или возведения временных конструкций. Перед тем как поступить на лущильный станок, древесина сначала пропаривается или погружается в бассейн с горячей водой. Это необходимо для того, чтобы из дерева были удалены смолы и деготь, а сами волокна стали более пластичными.
Процедура изготовления и отделки шпона.
После пропаривания, заготовки поступают на лущильный станок. Здесь бревно зажимается как в токарном станке в двух центрах, и начинает вращение вокруг оси. Нож шириной во всю длину бревна начинает снимать шпон. Эта процедура напоминает разматывание рулона бумаги. Только вместо бумаги получается полотно из шпона толщиной 1-1,4 мм. В изготовлении фанеры высокого качества необходимо чтобы шпон был одной толщины по всей длине отрезка.
Технологический процесс производства.
Следующим технологическим процессом производства выступает проверка целостности шпона. При обнаружении дефектов, таких как сучки или червоточины, они на специальном станке удаляются, а вместо них устанавливается заплата. С этого момента оборудование для производства фанеры практически исключает ручной труд, все остальные операции выполняются станками. Первым этапом идет сушка в туннельной сушилке. Листы, проходя по конвейеру обдуваются горячим воздухом, на выходе влажность древесины должна быть не более чем 4%.
Из полученного шпона дальше идет формирование массы фанеры. В зависимости от типа клеевого состава осуществляется склеивание слоев в определенном порядке – при использовании натуральных составов клеем покрываются только четные слои шпона. Для конструкционных и влагостойких типов фанеры применяются синтетические типы клея. Здесь клей наносится на все слои шпона. Нанесение клеевого состава при изготовлении фанеры производится при помощи специального станка, здесь клей наносится ровным слоем по всей поверхности листа.
Машина-автомат самостоятельно склеивает полотна шпона, чередуя слои так, чтобы волокна соседних слоев были взаимно перпендикулярны. Это обязательное условие получения качественной продукции.
В зависимости от используемой рецептуры клея изготовление фанеры осуществляется с помощью технологии холодной или горячей (термической) обработки под давлением.
При холодной технологии склеивания полотна шпона склеиваются и помещаются под пресс при обычной температуре. Через 6-8 часов находясь под прессом, клей надежно соединяет пласты.
При горячей технологии склеивания слои шпона с нанесенным составом помещаются под горячий пресс. Здесь высыхание клея осуществляется при температуре 60-80 градусов.
Для нанесения декоративного или специального покрытия применяются различные технологии и материалы. Чаще всего гладкое защитное покрытие наносится в виде слоя пластика. Лист полимерного материала приклеивается на поверхность при помощи клея на основе синтетической смолы. Для получения поверхности с определенной текстурой применяется технология горячего тиснения, когда слой смолы наносится на фанерный лист, а после этого во время просушивания осуществляет тиснение нужного рисунка на поверхности.
Производство мебели
Производство мебели на предприятии начинается с доставки закупленного леса. Круглый лес с помощью гидравлических манипуляторов разгружается в штабеля и подается на эстакады перед пилорамами — станками с ленточными пилами, где дерево распиливается на доски. После этого они подаются на станки для изготовления деревянных брусов с прямоугольным сечением. На этом этапе также происходит сортировка заготовок и удаления дефектов (сучков, гнили и т.п.).
Брусы складируют на поддоны и пропаривают в специальных камерах. Под действием пара древесина меняет цвет и улучшаются ее физико-механические свойства.
Поддоны с заготовками размещаются на сушильном полигоне — это открытая территория, где под действием солнца и ветра дерево высыхает естественным путем (этот этап длится 20-25 дней).
После этого заготовку высушивают в герметичных сушильных камерах. Чтобы достичь оптимальной влажности (10% +/- 2%), под контролем древесина равномерно увлажняется и сушится в течение 30-60 дней. В древесину монтируются специальные датчики, которые посылают на консоль управления информацию о влажности и температуре, что позволяет оператору управлять процессом.
Обязательным пунктом изготовления мебели является контроль качества заготовок. Квалифицированные работники отбирают заготовки с дефектами (сучки, кривизна, гниль, трещины), они непригодны для дальнейшего производства.
Заготовки, которые прошли контроль, сортируют по текстуре и цвету и подают на станок для формирования шипов и нанесения клея. Затем на линиях с высокой скоростью, заготовки прилегают друг к другу и склеиваются в ламели заданной длины. После этого их избавляют от остатков клея и неровностей, окончательно подбирают по фактуре и цвету и отправляют на линию склеивания щитов по ширине. Специальные станки наносят клей и под давлением 200 атм формируют щиты заданных размеров.
В этом случае мы получаем срощенный щит.
Как делают мебель из массива?
Для изготовления цельноламельного щита процесс тот же, но пропускается этап склейки ламелей в длину, так как они уже подбираются нужной
длины и при этом остаются целостными. Из-за этого такой щит, а отсюда и деталь, изготовлена из него, не может быть длиннее 2м.
Щит готов. Он является главным полуфабрикатом для изготовления почти всех изделий из дерева. На нашем предприятии дальше он отправляется в мебельный цех, где проходит еще несколько этапов обработки:
В специальную программу вносят необходимые параметры будущих деталей. Программа автоматически определяет размещение деталей на щите и запускает станок для раскроя.
Далее проводится механическая обработка выкроенных деталей (высверливают отверстия, пазы, снимают фаски, обрабатывают периметр и т.д.).
Следующим этапом является ручная шпатлевка деталей для обработки микротрещин и мелких сучков.
Обработанные детали обязательно шлифуют в три этапа:
автоматизированная обработка сторон детали
ручная обработка частей деталей;
плоское шлифование поверхностей деталей.
Финальной стадией изготовления мебели является покрытие деталей, которое включает в себя покраску или нанесение масла. Эти работы осуществляются вручную.
Готовые детали вместе с фурнитурой и дополнительными материалами упаковывают в картонные коробки, удобные для транспортировки и переноски. В каждую коробку обязательно вкладывают инструкцию для сборки, что делает возможным самостоятельный монтаж мебели.
Производство тары
Тара — это основной элемент упаковки, представляющий собой изделие для размещения продукции. Это емкость для хранения, упаковки и транспортировки промышленных товаров и сельскохозяйственных продуктов. В современной промышленности, пожалуй, не существует ни одной отрасли, где не приходится сталкиваться с тарой.
Тара подразделяется:
по материалу: на деревянную, пластмассовую, металлическую, стеклянную;
по размерам: на крупногабаритную и малогабаритную;
по обороту: на разовую, возвратную, многооборотную;
по конструктивной жесткости: на жесткую, мягкую и полужесткую;
по монтажным признакам: на неразборную, разборную, складную и разборно-складную;
по функциональному назначению: на транспортную и потребительскую;
по принадлежности к условиям использования: на производственную, инвентарную и складскую.
Деревянная тара по праву занимает одно из лидирующих мест среди всех видов упаковки. Ежегодно, на изготовление тары из дерева расходуется сотни миллионов кубометров древесины.
Основные виды деревянной тары :
Поддоны (паллеты)
Ящики, короба, коробки
Паллетные борта
Кабельные барабаны и катушки
Основной целью данного методического пособия является стремление разобраться в различных видах деревянной тары, способах ее изготовления и возможностях применения специальных инструментов для совершенствования технологий изготовления, увеличения производительности труда, снижения себестоимости изделия.
Из чего делают деревянную тару?
Деревянную упаковку производят из древесины хвойных и лиственных пород. Из хвойных деревьев получают прочное, устойчивое к гниению сырье. Такой материал легко поддается обработке. Лиственные пиломатериалы разнообразны по свойствам и широко применяются. Однако такое сырье перед использованием нужно тщательно просушить и обработать антисептиком. Вид древесины подбирают с учетом продукции, для которой предназначена упаковка. К примеру, тару из сосны не используют для перевозки продовольствия. Сосна имеет интенсивный смоляной запах, который передает упакованному товару.
Как производят деревянную тару
Производство деревянных ящиков происходит в несколько этапов. Сперва заготавливают бревна, очищают их от сучьев и коры. Затем сырье распиливают с помощью специального оборудования. В результате получают брусья и доски, из которых производится деревянная тара. Пиломатериалы должны быть высокого качества, без гнили и трещин. Все дефекты древесины проявляются при контроле качества готовых изделий. Учитывается внешний вид упаковки, дефекты материала, нормы и правила, регулирующие производство деревянной тары. Для того, чтобы продлить срок службы изделия, применяют специальные красящие и антисептические составы.
Как правило, используются такие породы деревьев, как береза, липа, тополь или ольха. Они быстро сохнут, хорошо горят, не дымят и не выделяют много смолы. С 2-3 деревьев можно получить 100 000 коробков спичек, в зависимости от типа древесины и толщины дерева.
Затем с помощью плотницкого станка из бревен вырезаются длинные тонкие слои, которые называются шпоном. Обычно спичечные соломинки и фанера изготавливаются из шпона. Для последнего несколько слоев шпона склеиваются между собой.
Изготовив сразу много листов шпона, рабочие передают их на станок, который быстро нарезает шпон на крошечные соломинки — основу для будущих спичек. Соломинки транспортируются с помощью конвейеров в теплый чан, где горячие стенки нагревают древесину так, что из нее испаряется лишняя влага, потому что сырыми спичками разжечь огонь нельзя.
Полностью высушенная спичечная солома переходит на следующий этап, где хитрые машины равномерно укладывают куски дерева. В этой форме соломинку закрепляют на одном конце, а другой опускают в расплавленную серу. После высыхания он обладает огнеопасным свойством.
Механическиё метод
При механическом получении древесной массы древесину, как правило, истирают или размалывают в водной среде. Под действием воды, тепла и специальных реагентов лигнин размягчается, и древесина распадается на отдельные волокна.
«Механическую» схему получения волокон целлюлозы можно описать примерно так. Промытая древесная щепа помещается в специальный рафинер, где измельчается и обрабатывается.
После очистки древесная масса готова для дальнейшей обработки. Поскольку, несмотря на обработку, лигнин не удаляется полностью, выход древесной массы получается высоким.
Наличие лигнина на поверхности и внутри волокон увеличивает их твердость и жесткость, а также придает им сравнительно стабильный размер.
Листы, полученные из «механической» древесной массы, имеют высокую пухлость и низкую плотность, то есть достаточно низкую массу единицы площади для данной толщины.
Это очень важно, поскольку отражается на технических и «экономических» показателях материала
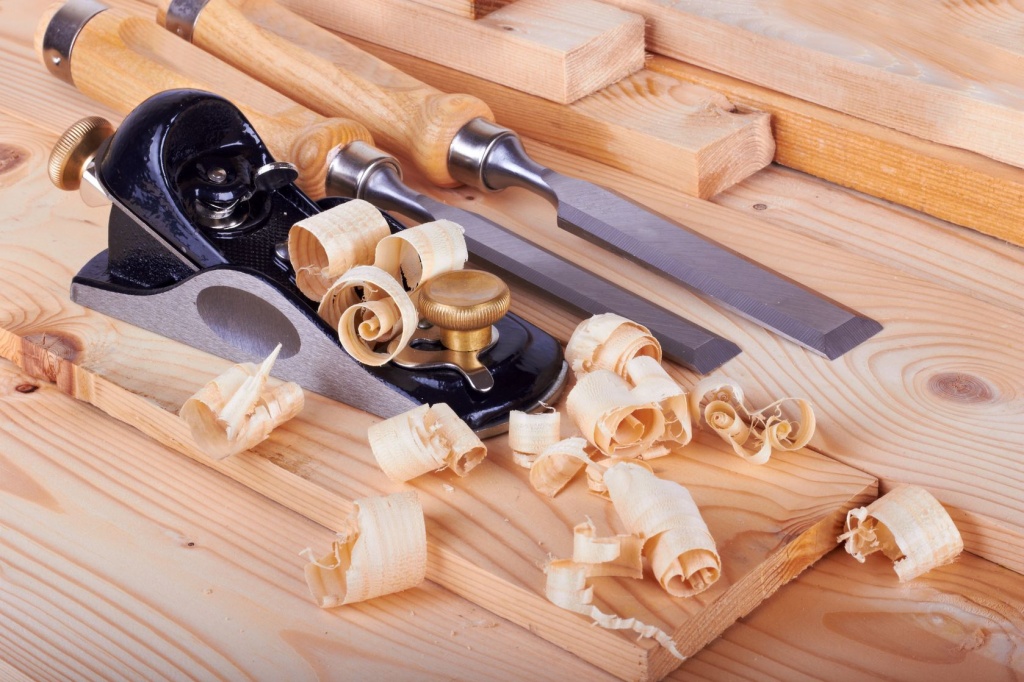
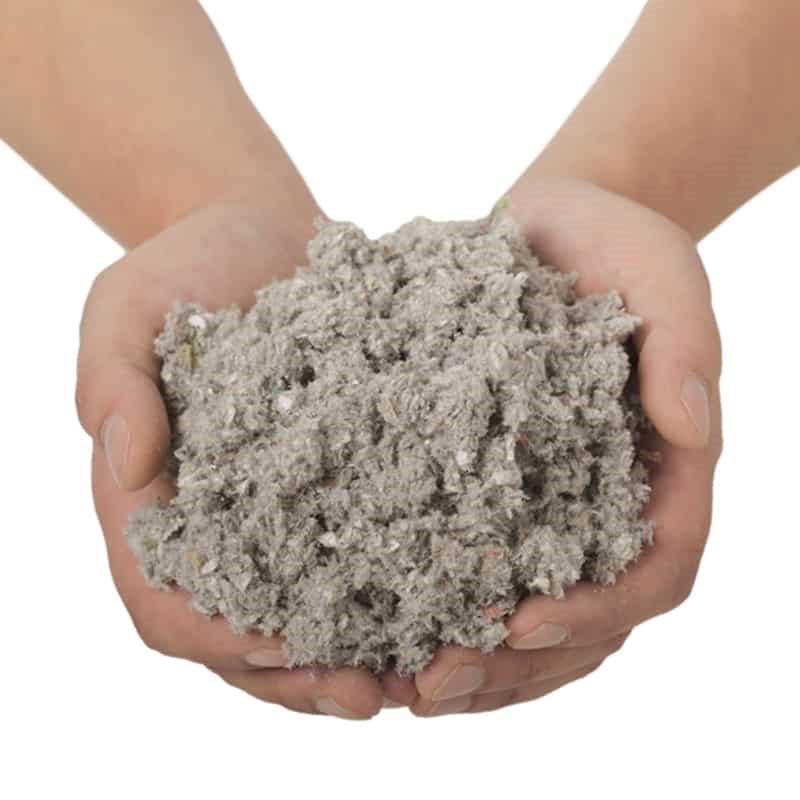
Целлюлозно-бумажная отрасль
в настоящее время на территории России осуществляют деятельность около 200 предприятий целлюлозно-бумажной промышленности. Отрасль выпускает:
Целлюлоза
Древесная целлюлоза остается основным сырьем для производства бумаги. Как правило, используется измельченная древесина сосны,
березы, тополя и клена. Реже для этих целей используются дуб, каштан, кедр и другие более ценные породы.
Древесная целлюлоза — это натуральное органическое соединение (волокно), получаемое путем варки измельченной древесной щепы. Целлюлоза является ключевым структурным элементом, составляющим оболочку растительной клетки. Волокно обладает удивительно высокой гибкостью и механической прочностью.
При производстве качественной бумаги невозможно обойтись без использования различного оборудования.
Оборудование для производства бумаги включает в себя, прежде всего, бумагоделательную машину. Это специальный агрегат, с помощью которого происходит производство бумажного полотна, так же ее последовательное прессование, отделка и сушка. Эта машина состоит из трех основных частей – сеточной, сушильной и прессовки, а также наката и каландра. Кроме того, он поставляется в комплекте с емкостями для смешивания компонентов и формирования исходной массы, контрольно-измерительными приборами, очистителями, специальными насосами и устройствами для обработки тех продуктов, которые были забракованы.
Помимо бумагоделательной машины, оборудование для производства бумаги включает в себя оборудование, проходя через которое исходный материал будет отличаться более высокой плотностью, лоском, гладкостью. Это делается с помощью так называемого суперкалендера, на выходе которого можно получить бумагу более высокого качества. После этого полученный материал попадает на резку, где его разрезают либо сразу на листы нужного формата, либо на огромные рулоны, которые поступают для упаковки в рулонно-упаковочную машину.
Важной составляющей современного оборудования для производства бумаги являются разнообразные проклеивающие машины, с помощью которых в исходное сырье вводятся различные добавки, позволяющие получить продукт с заданными свойствами (влагостойкость, повышенная прочность или эластичность, стойкость к стиранию).
Процесс производства картона состоит из нескольких основных этапов:
Работа с сырьем. На этом этапе выбирается подходящий рабочий материал. Чаще всего это остатки древесины, которые шли на те или иные производственные нужны.
Обработка сырья. Бревна обрабатываются в специальном оборудовании, где кора отделяется от древесины. Далее дерево измельчается на мелкие щепки.
Варка. Полученную щепу варят в химическом растворе, после чего она превращается в целлюлозную массу.
Промывание. Этот этап предполагает отделение от целлюлозной массы любых других элементов – мусора, непроваренных щепок и т.д. Чистую массу выливают на сетку, на которой из целлюлозы вытекает лишняя вода.
Выжимание. Полученное полотно зажимают валами, чтобы убрать оставшуюся воду.
Сушка. Далее нужно лишь высушить материал и разрезать его на необходимый формат.
Как видно, технология производства картона требует наличия большого количества специального оборудования, поэтому этот процесс считается достаточно сложным.
Чтобы сделать картон более плотным, при его производстве к щепе могут добавлять клеящие вещества, различные минеральные и химические волокна, макулатуру и т.д.
Производство вискозного волокна состоит из двух последовательных стадий: получение прядильной массы — вискозы и формование волокна. В качестве сырья используется древесная целлюлоза, содержащая 95—99 % высокомолекулярной волокнообразующей фракции со степенью полимеризации 800—1100.
Получение вискозы
Получение вискозы включает следующие операции:
Выделение целлюлозы из древесины. Поскольку в древесине на целлюлозу приходится лишь половина массы, сначала целлюлозу извлекают. Для этого древесину помещают в раствор гидросульфита кальция и варят под давлением в закрытых котлах в течение 24 часов. При этом разрушаются связи между волоконцами целлюлозы. Затем к целлюлозе добавляют воду и наносят её на конвейер. После этого её сушат и режут на листы. Получается сульфитная целлюлоза, которая идёт как на производство бумаги, так и на производство вискозы.
Обработка целлюлозы 20%-м раствором гидроксида магния (мерсеризация) в течение 5—115 минут при температуре +45…+60 °С. При этом образуется аддитивное соединение целлюлозы с щёлочью: (щелочная целлюлоза) (а) и алкоголяты целлюлозы (б). Одновременно с реакциями (а) и (б) при мерсеризации происходит набухание целлюлозы и растворение гемицеллюлоз, что способствует диффузии этерифицирующего агента внутрь волокна при последующем ксантогенировании щелочной целлюлозы.
Отжим суспензии для удаления избытка раствора гидроксида натрия на отжимном прессе до степени отжима (отношение масс отжатой щелочной целлюлозы и суспензии) 0,33-0,36.
Измельчение отжатой щелочной целлюлозы.
Окислительная деструкция (предсозревание) щелочной целлюлозы за счёт окисления её кислородом воздуха на транспортере или в специальных аппаратах в течение 1,5—2 часов при температуре +50…+60 °C. В процессе предсозревания степень полимеризации целлюлозы снижается до 400—600.
Ксантогенирование. Процесс ксантогенирования заключается в обработке щелочной целлюлозы, при этом образуется новое химическое соединение — ксантогенат целлюлозы, способный раствориться в разбавленном растворе едкого натра.
Перевод целлюлозы в раствор, получение вискозы. В результате обработки целлюлозы концентрированным раствором гидроксида натрия и сероуглеродом на предыдущих стадиях она приобретает способность переходить в раствор, необходимую для формования волокна. Целлюлозу растворяют в 4%-м растворе гидроксида натрия и выдерживают в течение нескольких суток, в результате чего она «созревает» — получается вискоза.
Полезно знать:
1. Устойчивое управление лесными ресурсами Устойчивое лесное хозяйство — ключ к сохранению экосистем и обеспечению долгосрочного сырьевого базиса для деревообрабатывающей промышленности. Знание и соблюдение стандартов FSC (Forest Stewardship Council) или PEFC (Programme for the Endorsement of Forest Certification) гарантирует, что продукция произведена из древесины, полученной из устойчиво управляемых лесов.
2. Технологии минимизации отходов Современные технологии позволяют максимально использовать каждый кусок древесины, минимизируя отходы. Примеры включают оптимизированные пилорамы, которые автоматически рассчитывают наилучший способ раскроя бревна, и системы переработки отходов на производство биотоплива.
3. Экологические аспекты производства Процессы, связанные с обработкой древесины, могут включать использование химических веществ, которые требуют особого внимания с точки зрения экологии. Знание и применение экологически чистых методов и материалов важно для снижения воздействия на окружающую среду.
4. Важность сертификации Сертификация продукции и производственных процессов по международным стандартам может значительно повысить доверие к бренду и увеличить рыночные возможности. Сертификация ISO, например, подтверждает соответствие управления качеством и экологическим стандартам.
5. Инновации и развитие технологий Внедрение инноваций и новых технологий, таких как цифровая автоматизация, улучшенное планирование ресурсов предприятия (ERP) и роботизированные производственные линии, может значительно улучшить эффективность производства и качество конечной продукции.
6. Повышение энергоэффективности Инвестиции в энергоэффективное оборудование и технологии не только снижают эксплуатационные расходы, но и уменьшают воздействие на окружающую среду. Использование возобновляемых источников энергии также способствует созданию зелёных производств.
7. Роль в экономике Деревообрабатывающие производства являются значительным источником рабочих мест и экономической активности, особенно в регионах, богатых лесными ресурсами. Понимание их роли в местной и глобальной экономике важно для стратегического планирования и развития отрасли.